Surface and center-driven fabric winders are two fabric winding machines used in the textile industry to roll the fabric onto a paper tube core. Each has its advantages and disadvantages based on its design, functionality, and the specific application it’s used for.
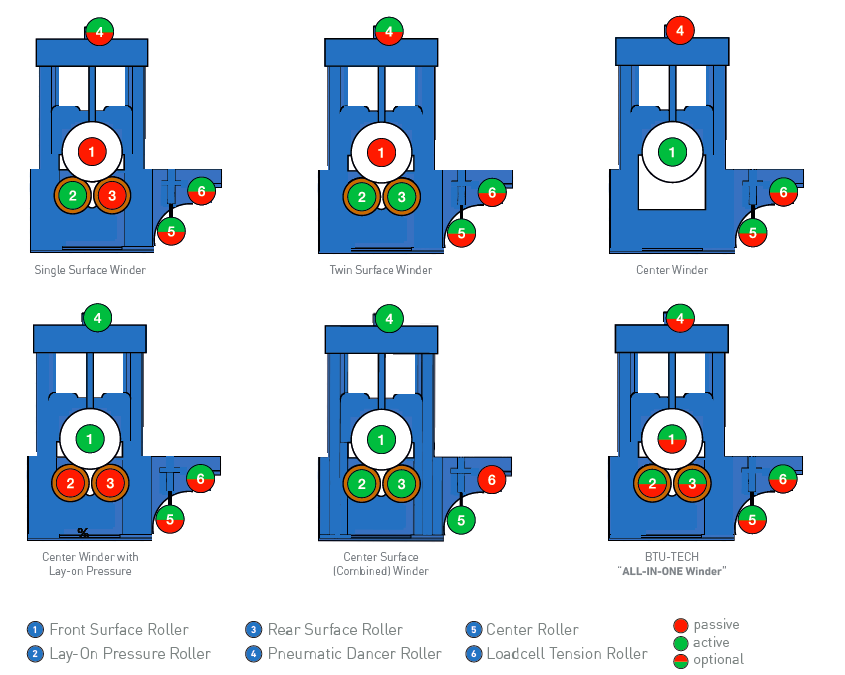
Surface Fabric Winders
Pros:
Gentle Handling: Surface winders are known for gently handling delicate fabrics. The fabric is not stretched as much because the winding tension is spread over a wider surface area.
Versatility: They can handle a variety of materials, including delicate and stretchy fabrics, without causing damage or deformation. Also, the roll weight is lifted by the winding rollers, so the roll is not bent by its weight, allowing it to wind much bigger rolls with a surface winder.
Adjustable Tension Control: These winders allow for better tension control, crucial for maintaining fabric quality and preventing wrinkles or distortions.

Cons:
Speed Limitations: Surface winders generally operate at lower speeds than center-driven winders, which might reduce overall productivity.
Min. Tension: Because of the required surface pressing drive roller, surface winders cannot get as loose tension as the center winders.
Complexity: They can be more complex and expensive due to the mechanisms required to maintain even tension and gentle handling.
Maintenance: More moving parts and contact surfaces can lead to higher maintenance requirements and costs.
Center Driven Fabric Winders
Pros:
High Speed: Center-driven winders can operate at higher speeds, making them suitable for high-volume production environments.
Simplicity: These winders are simpler in design and operation, potentially leading to lower initial investment and maintenance costs.
Efficiency: They are often more efficient for long runs of material.
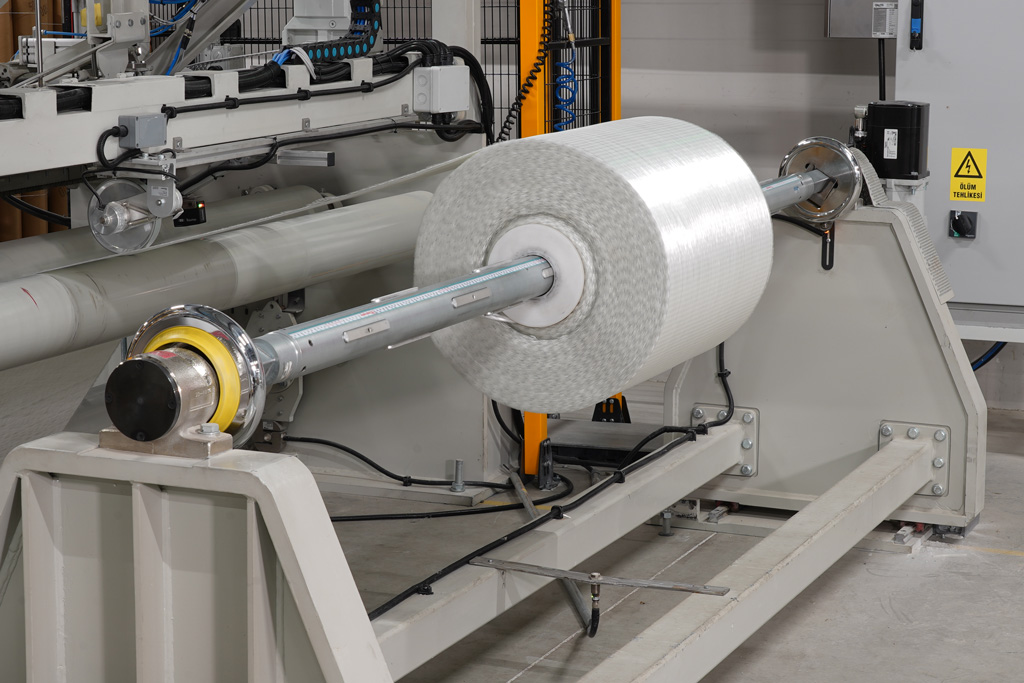
Cons:
Tension Control: Maintaining uniform tension across the fabric can be more challenging, especially for stretchy or delicate materials, which can lead to quality issues.
Less Versatility: Center-driven winders may not be as suitable for delicate or stretchy fabrics, as the tension is applied directly to the roll’s core, potentially stretching or damaging the material.
Wrinkling Risk: There’s a higher risk of wrinkling or distorting the fabric, mainly if tension is not managed correctly or the fabric is particularly sensitive.
Bending: As the roll weight increases, the shaft begins to bend, creating wrinkles, telescope effects, etc. The roll needs to be supported with rollers underneath.
In choosing between the two, it’s essential to consider the specific needs of your production, including the type of fabric you’re working with, the required speed and volume of production, and the quality demands of the finished product. Each type has its place, and the best choice often depends on a balance of these factors.
Combined Winders, a solution to cons of both types of winders?
Combined fabric winders, which can run in a combination of surface and center winding modes, can be the right solution in cases where various fabric types are wound on the textile line. Adding a shaft lift pressure, which acts as a lay-on roll nip, introduces additional tightness.

BTU-TECH has created an innovative winding platform for addressing all of the industry needs: “All-in-One Winder.”
The full version of “BTU-TECH All-in-One Winder” can run in all three modes (surface, center, lift pressure, and combined). In addition, this winder can be ordered with either of the features with the optimum investment. Later, it can be upgraded to include the missing features for the new fabric winding challenges.
Pay a visit to the “All-in-One Winder” webpage for a detailed product video and brochure.